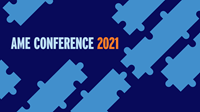
CONFERENCE SPEAKERS
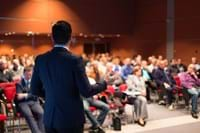
KEYNOTES
Back to Basics: Understanding the Past State
Presentation Overview
Over the decades it has been proven to be difficult to move Lean forward from a niche management practice to one that is commonly found in organizations of all types. This presentation will highlight research conducted over the last 13 years to unravel the mystery of why most CEOs remain fully committed to archaic classical management. It is only by understanding the ways and means by which the past retains its grip on the present that greater progress in management thinking and practice can be achieved.
Presenter: Bob Emiliani, professor, author, researcher, and historian of progressive management
Dr. Bob Emiliani has been a Lean practitioner and professor of Lean management for over 25 years. Prior joining academia, he worked in industry for 15 years and had management responsibility in engineering, manufacturing and supply chain management. Bob was part of a team responsible for implementing Lean principles and practices in both manufacturing and supply chains at Pratt & Whitney. He was the first academic to establish a research agenda focused on Lean leadership, resulting in numerous publications and varied leadership development workshops. Bob is a prolific, versatile, and award-winning writer whose publications span engineering, business, social sciences, and humanities. He has authored 24 books and dozens of research papers across six different disciplines. His work on Lean leadership and Lean as applied to higher education are widely recognized. Bob created an innovative, process-based understanding of leadership called “Speed Leadership.” His most recent work uncovers the network of factors that impede the advancement of Lean management. Please visit www.bobemiliani.com
Developing Enterprise Excellence in Problem Solving – The Art of Excellence
Presentation Overview
Enterprise Excellence focuses on bringing all aspects of an organization into the same improvement and management system. Operations, Sales, New Product Development, Finance, Human resources—even IT—need to embrace the skill of deliberate practice and exercise scientific thinking embracing standard problem-solving methodologies.
Becoming an effective, confident, and competent problem solver is a complex process that requires a range of skills and experience. The keynote will demonstrate how leaders can support practical problem solving explicitly and repeatedly provide employees with opportunities to develop critical problem-solving skills.
Presenter: Billy Taylor, business executive, dynamic speaker and leadership guru
Billy Taylor is business executive, dynamic speaker and leadership guru. He is the CEO of LinkedXL (Excellence), a business operation systems architecting firm. Billy Taylor is a disciple of continuous improvement processes and a certified Six Sigma Black Belt business leader.
During his 30 years with Goodyear Tires, he served as director of North America manufacturing and chief diversity and inclusion officer, where he led diversity and inclusion strategies for 64,000 employees across 22 countries.
He is a highly rated AME Conference keynote speaker. Recently, Billy Taylor joined AME’s management team as global head of inclusion, equity and diversity (IE&D). In this volunteer role, he will work with the AME president and CEO and lead the organization in supporting an inclusive environment for board members, staff, volunteers, partners and members to make sure all voices are heard. Billy Taylor will be responsible for guiding the organization, identifying ways to attract diverse candidates for volunteer and board roles and developing programs that foster a collaborative environment to drive innovation.
Learning to Lead, Leading to Learn: How Intentional Leadership Helps You Solve More Problems and Engage More People
Presentation Overview
Too often our world is focused on generating more … producing more output, generating more revenue, providing more service.
But what achieving more didn’t come from doing more, but rather from the ability to learn more effectively how to solve problems and engage everyone at all levels?
In this keynote you will discover the secrets to creating a people-centred culture of learning. Katie Anderson will highlight the fundamental practices of a leader, highlighted in her best-selling book Learning to Lead, Leading to Learn, and understand the importance of intention and reflection as the foundation of solving more problems and engaging more people.
Be inspired to lead -- and live with greater intention. Walk away with three tangible practices that you can begin immediately to lead to learn, to solve problems, and support your people.
Presenter: Katie Anderson, internationally recognized leadership coach, author, consultant and professional speaker
Katie Anderson is an internationally recognized leadership coach, consultant and professional speaker, best known for inspiring individuals and organizations to lead with intention. She helps leaders at levels and organizations of all sizes to connect purpose, process and practice to achieve higher levels of performance. Anderson is passionate about helping people around the world learn to lead and lead to learn. Her first non-fiction book, "Learning to Lead, Leading to Learn: Lessons from Toyota Leader Isao Yoshino on a Lifetime of Continuous Learning," debuted in July 2020 as an international Amazon #1 new release.
Be the Leader you are Capable of Becoming
Presentation Overview
Most of us strive to become better at what we do. But there is a depressingly small number of leaders who are very good at passionately engaging people in highly effective improvement practices. What do they do differently from the rest? Is there a model we can use to help us get better? Based on my conversations and observations with some of these leaders I believe the answer is yes. In this talk I plan to share four behaviors these leaders practiced to become a better leader. They successfully improved their abilities to elevate both the magnitude and rate of improvement with their team, their peers and their organization (e.g., at getting better, at getting better).
Presenter: Michael Bremer, Author "How to Do a Gemba Walk" a Shingo Research & Professional Publication Award recipient
Michael Bremer has been an active AME member since 1992. He has served as vice president of the AME Excellence Awards program since 2010 and as AME’s CFO from 2002 – 2010. As a volunteer, he led the redesign of AME’s performance excellence criteria and has served on both the AME national board and management teams. He recently joined the Advisory Council for Dominican University’s Osher Lifelong Learning Institute program in San Rafael, Calif.
He has co-authored three books on effective performance improvement practices and wrote the Shingo Award-winning book, “How to Do a Gemba Walk.” He was recognized as AME's 2019 Mac McCulloch Lifetime Achievement Award Recipient.
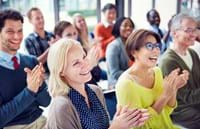
PRACTITIONERS
Building Structure Amidst Disruption: A3 Thinking and Strategy Deployment
Presentation Overview
Businesses and Leaders are constantly challenged by external events and market disruptions. The year 2020 and the COVID pandemic has reminded us all that we are not in control of our external environment. We can, however, establish structure within our businesses that can provide our teams with familiarity and a solid foundation to weather the storms that that we experience. A3 Thinking and Strategy Deployment provide that foundation and build leaders even while operating amidst external uncertainty. This session will discuss the challenges and opportunities of establishing A3 and SD mindsets and processes during a disruptive environment.
Presenter: Bart Reimer, Vice President of Operations at Charter Steel
Bart has over 30 years of experience in manufacturing and operations, all in materials related industries, including 20 years in brick and refractory manufacturing, 8 years with Goodyear Tire & Rubber and 3 years in the iron and steel industry with Charter Manufacturing. He is currently the Vice President of Operations with Charter Steel which has 6 plants in Wisconsin and Ohio and a strong culture based on people, trust, safety and continuous improvement. His passion is setting strategy, establishing process and building leaders and teams that win.
The Tailed Fishbone: Add a Tail to your Root Cause Analysis to Solve Problems and Sustain Improvement Efforts
Presentation Overview
Do you find your improvement efforts get bogged down in action items? Do improvement efforts fail to see actions completed? Are partially implemented improvements successful? Sustainable? Do you get nervous and/or struggle when it comes time to facilitate Root Cause Analysis?
Let me introduce to you the Tailed Fishbone. A methodology at facilitating Root Cause Analysis that makes getting to Root Cause simpler and with greater clarity. A method that reduces the effort both for the facilitator and the team members allowing for a more successful and sustainable initiative.
Presenter: Mark Adams, Director Customer Experience - Agility Business Group at Flex
Mark is a process improvement enthusiast who has been facilitating the change management process for a dozen years. Mark has facilitated strategy deployment and continuous improvement supporting industries such as Manufacturing, Training, Operations, Aerospace, Solar/Energy, Recruiting, Maintenance, Medical and other diverse fields. His passion lies in teaching and coaching continuous improvement that fits into an organization’s culture and needs. Mark serves as Director of Customer Experience and is responsible for customer surveys and feedback analysis. With the utilization of Lean and Six Sigma tool sets, Mark identifies Voice of Customer using the voice of the customer to improve, the customer journey within Flex's Agility Business Group. Mark earned his Bachelor of Science in Management at Wayland Baptist University, his Executive Master of Business Administration jointly delivered by the Universities of Kentucky and Louisville, and earned his Lean Six Sigma Black Belt through the United States Air Force.
Kata and Problem Solving
Presentation Overview
The Debden Printing site, where all English banknotes are manufactured, underwent significant transformation in the early 2010’s. All the +20 year old printing machines were upgraded for state of the art equipment; the banknotes changed from paper to polymer -based. Man, machines, materials – all had to undergo change. In this turbulent environment, problem solving became a daily, if not hourly, necessity.
This presentation will focus on how a problem solving culture was developed and embedded – the mistakes made and lessons learnt – and ultimately show how two key techniques were able to unlock employee engagement and ingenuity.
Presenter: Iain Stewart, Manufacturing Manager at Tarmac Building Product
Iain Stewart is the Manufacturing Manager at Tarmac’s Aircrete Building Products site in Essex. Iain joined Tarmac in June 2020 and is responsible for improving manufacturing processes across both factories in line with Safety, Quality, Cost, Delivery, Machine and People deliverables. He also manages the Quality/Technical department in driving right first time and reducing quality rejects & scrap. Iain is playing a key role in setting the strategic vision to ensure the site has a viable future.
Prior to joining Tarmac, Iain has held a variety of operational roles within the manufacturing sector working in Pharmaceuticals, FMCG and Security Print. These roles have ranged from production scale-up/support to continuous improvement, lean implementation, coaching and problem solving. Iain earned a PhD in Catalysis from the University of Liverpool in 1999 and a Bachelor of Science degree in Applied Chemistry from Strathclyde University. He splits his time equally between his wife and 2 children.
Presenter: Steve Craig, Steve Craig, Managing Director at Komori
Steve Craig is the MD of Komori Currency Technology. He is responsible for growing sales in the EMEA region, and for driving innovation through partnerships with leaders inside and outside the banknote. Steve’s passion is working with customers to drive their quality and productivity through lean techniques, with a clear focus on culture.
Steve joined the Bank of England Printing Works in Debden as Quality Manager in 1998, and was part of the team responsible for the privatisation of the facility in 2003. Subsequently joining De la Rue, Steve worked in various Technical, Operational and leadership roles. He has driven change and productivity through lean processes in the UK, Malta, South Africa, and Kenya.
Steve returned to Debden in 2012 to lead the site in a transformation that included the installation of two Komori banknote lines, and the successful launch of the Bank of England’s £5, £10 and £20 polymer banknotes. As part of the innovation involved in these launches, Debden won the UK Works Management Award in 2015 for their Polymer handling machine, and in 2018 hosted UK best practice visits showcasing their work on asset care and Toyota Kata.
The Hard Yards of Continuous Improvement
Presentation Overview
A significant part of the role of a Lean Leader is to create an environment whereby continuous improvement (kata) can be coached and performance visualised such that the extended team can engage fully.
Where to start? What that looks and feels like? and How to sustain improvement for stability first, then genuine and sustainable improvement thereafter?
Presenter: Jim Glover, Group Manager - Continuous Improvement at Visy
Jim Glover is a passionate LEAN leader and has been a practitioner and advocate of Continuous Improvement globally for around 30 years. Jim is currently Group C.I. Manager for VISY and he has previously held senior CI roles at Boeing, Futuris Automotive where he helped drive the Futuris Global Production System and more recently at Vistaprint guiding the Derrimut site to become the first Australian recipient of a Shingo Award for Operational Excellence in 2014.There will the opportunity for those attending to ask questions and also share some learning from their own Kaizen spirit development.
Align Your Organsiation - What's Your DNA?
Presentation Overview
In the new post-pandemic business world of ‘working from anywhere’, traditional organisational alignment in shared physical workspaces is disappearing. Methods of communicating a common direction are fast diminishing. A new approach to alignment is called for, bringing together our human needs for purpose, clarity and creativity. Combining a little neuroscience and psychology – using our strongest human sense - provides a powerful way to define / align our organisational DNA for the future. Let’s Get Visual and ensure our passion, mission, and vision for the future is clearly visible to all our stakeholders.
Presenter: David Stannard, Chief Visionary Officer atThe Vision Guy - Paradise Rescued
David Stannard is the Founder Director of niche Bordeaux wine producer Paradise Rescued, hand producing fine organic wine and sustaining the rural heritage of the village of Cardan Bordeaux France.
Visionary and optimist, The Vision Guy helps people and organisations to develop and communicate their visions through pictures. He is a passionate advocate on the use of pictures and visual management, creator of the Success Trifecta, DNA model and picture Visions.
David is a chemical engineer and highly experienced manufacturing leader with a demonstrated history of achievement in the international petrochemical industry across many business functions. He is a three-time book Author, Public Speaker and Workshop Leader.
Improving Safety Through Breakthrough Methodology and Solutions
Presentation Overview
With a goal to reduce injuries by half, a mining operation took a unique approach to safety improvements. Through collaboration, a diverse team applied a ‘Define, Measure, Analyze, Improve and Control’ Kaizen business improvement methodology, a well-proven methodology typically used for production and cost projects, to identify 20 high-risk manual handling and tooling-related activities. As a result, the site has sustained over 12 months without any recordable hand injuries and reduced its All Injury Frequency Rate by 65 per cent. The session will discuss the Kaizen approach; (the preparation, the Event & follow-up activities); including learnings (plus / deltas) , change management & results.
Presenter: Patrick Antoskiewicz, Executive Manager, Planning & Transformation, NBN Australia
Senior transformation leader with an outstanding track-record in designing & delivering business transformation to improve customer experience and drive operational efficiencies. Known to turn chaos into order by bringing a structured approach to challenges using data and process. Industry Award-winner for Innovation. An authentic people leader passionate about building high performing and engaged teams.
Managing Complex Business Challenge using a KPI Tree. A Practical Approach to “Divide and Conquer”
Presentation Overview
How often does your business want to tackle an issue but does not know where to start? If a team works on something, what would be the impact towards the overall business objective? How do you set coherent targets that cascade down, and then back up? In this user case, we are going to see how we can implement a sound structure in order to solve a complex problem and drive improvement one step at a time, by dividing, and conquering.
Presenter: Kevin Bennar, Process Excellence Manager at Note Printing Australia
Kevin Bennar has a strong history of orchestrating successful process improvement activities and lean initiatives designed to increase revenue. He started his career as a mechanical engineer and quickly transitioned towards manufacturing efficiency and continuous improvement methodology such as Lean, 6 Sigma and Theory Of Constraints. He had the chance to learn from the European automotive and aerospace sectors before recently moving to Australia. After joining Note Printing Australia, he quickly moved to the role of Process Excellence Manager where he has been driving major initiatives for the business since then.
Embedding DMAIC Thinking: Improving our Identification and Management of Complex Problems and Key Projects
Presentation Overview
Without a robust system for identifying key improvement opportunities, substantial energy can be directed into solving complex problems and deploying projects that are perceived to be major contributors to waste and inefficiency, but won’t result in significant benefits to the business. We will detail how the DMAIC process was set up from a zero base and utilised in concert with a visual management system to improve the identification of key projects, manage progress, and capture the benefits from implementation. You will get an insight on the lessons learned, successes and failures and where next.
Presenter: Luke Maguire, Quality Compliance and Process Engineering Manager at Note Printing Australia
Luke Maguire is the Quality Compliance and Process Engineering Manager at Note Printing Australia, leading a team focused on improving NPA’s process capability and quality systems. In this role, he is leading efficiency and continuous improvement projects using Lean six sigma methodologies, with a focus on product quality and spoilage reduction. Luke has been involved in the banknote industry for over a decade, having previously worked as a Research Scientist and Quality Manager at the Reserve Bank of Australia, and has a PhD in Physics.
Our TLSC Journey: Surface Understanding
Presentation Overview
Having launched Australia’s newly upgraded banknotes, NPA’s people and process capability had to adapt to new and complex problems to improve their way of life. Through NPA’s Business Excellence drive, in late 2019 their Technical Services Team embarked on the reinvention of their process mapping. It wasn’t long until their understanding grew into the makings of an end to end product development process map for the business, known as a Total Link System Chart (TLSC). Through problem solving, the team were driven to surface enough understanding of the process to lead and liberate business-wide understanding on a number of levels. This presentation will take you through the journey that took them there.
Presenter: Robert Cook, Design Manager at Note Printing Australia
Robert Cook is Design Manager at Note Printing Australia and is responsible for the facilitation of conceptual design solutions for NPA’s security printing products. Rob comes from a fine arts background and commenced at NPA in 2006 as a Keyline Artist, a role responsible for the illustration of highly detailed drawings for Banknotes, Passports and secure documents. Producing artwork for a number of countries, including Australia, Brunei, Chile, Singapore, Solomon Islands, and Vanuatu. Since 2019 Rob transitioned to the Design Manger role to focus on NPA’s design process and its product and service offering.
Our Digital Home Loan Originations Journey
Presentation Overview
The home loan lending landscape is super competitive and rapidly changing. Banks and lenders must continue to invest big and find new ways to compete to stay relevant in a digital world.
Sam Gosios is strategically driving change in his bank so it becomes more competitive in home lending by leveraging automation that transforms the end to end loan originations processes bringing to life a digitally enabled lender of tomorrow.
This presentation will take you through the current journey where ME Bank are moving rapidly from tactical process improvements to strategic service enhancements through smart automation and digitisation in home lending.
Presenter: Sam Gosios – Senior Product Owner, Lending Operations
Sam Gosios is an experienced financial services and professional services executive. He joined ME in March 2020 and is responsible for digitising the home loan originations service, end to end.
Before joining ME, he held senior roles at Catholic Super, IQ Group, Kinetic Super, Mercer, Superpartners and HOSTPLUS.
His career has spanned Australia, New Zealand and Fiji where he has managed large projects, led business units and large teams through complex change and automation programs.
Most recently Sam has worked on a large strategic initiative to plan, design and deliver an optimal digitised home loan originations service for his bank.
Sam holds a Bachelor of Science with Honours and a Masters in Finance. He is a promoter for meaningful change, and oriented towards innovation.
Problem Solving when Leading Transformation
Presentation Overview
Part of leading through change is dealing with problems. Not all problems are created equal. Particularly, wicked problems. Developing the skill to diagnose a problem, learning to articulate a problem and adjusting the approach to solve it is a fundamental skill that unlocks potential to move faster and infuses empowerment in your teams. Not too far behind is the skill to anticipate a problem and develop mitigation plans to overcome it.
This session covers some practical learnings and two simple Problem solving frameworks that stand the passage of time across various practical examples of business challenges
Presenter: Yelitza Guerra, GM Distribution & Logistics ANZ and SEA Operations at Device Technologies
Yelitza is regionally responsible for Planning, Logistics Operations, Distribution at Device Technologies. An Economist by formation, Yelitza holds a MBA(Executive) from the University of New South Wales and is certified Six Sigma Green Belt with over 20 years of experience across Operations, and Procurement . During her career, she has worked in various industries including Medical Devices and Technology and has developed broad experience leading teams across fast paced accelerated change and business transformation. Her approach enables team and functional readiness for new process and technologies across the supply chain.
Recognised for her collaborative and inclusive approach, she has also served as a mentor and advisor within the Supply Chain community.
Engaging Front Line Staff in your Operational Excellence Journey
Presentation Overview
In our journey towards the goal of creating an operational excellence environment, we’re collectively not short of the tools and how to deploy them but the real challenge is to engage our front line people in the journey. How do we “win the hearts and minds” of our most valuable asset, whereby they’re eager to be part of the solution?
Working on this challenge over the years within global organisations, Paul will share from his experience, keys that will bring a new depth of engagement which will produce valuable momentum towards your OPEX goal.
Presenter: Paul Deane, Business Improvement Lead QLD, Network Optimisation & Business Efficiency at Australia Post
An innovative continuous Improvement practitioner, with strengths in LEAN systems, ISO9001, manufacturing best practice and DMAIC projects with CSSC Certified GE 6 Sigma Black and Green Belts. Over 10+ years implementing OPEX systems from zero base within global organisations developing strong insight into engaging front line staff.
25+ years working with large global organisations in Australia, NZ, Malaysia and UAE leading manufacturing and service operations of small and large teams, successfully deploying business improvement methodologies, working cross-functionally with sales/marketing, engineering & R&D teams.
His operational, service and manufacturing experience has covered chemical, industrial and food industries.
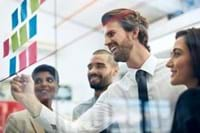
WORKSHOPS
Critical Thinking is not Something your Mind Does; it is Something You Do with your Mind.
Workshop Overview
The Critical Thinking Workshop will be an education about one of the most valuable of all human mental capabilities – the ability to think about thinking. In essence the process of organising human beings needs to discourage too much thinking to enable convergence and reduce variability. The vast majority of people love the feeling of order; making critical thinking largely an unnatural act. Ironically that same majority will intuitively follow leaders who think better than they do and who they can trust to do all the hard thinking.
We’ll be exploring what critical thinking is and what it is not. How to learn how to do it and how to recognise whether people will or won’t do it.
Presenter: Errol Benvie, Founder and Director at Wisdomlab
Errol is founder and Director of the Wisdomlab, an organisational and leadership consultancy specialising in thinking differently and changing perspectives across every facet of the organisation. The competitive frontier in complexity and uncertainty will be the ability to optimise human ingenuity and self-determination. Errol’s practice is grounded by a senior leadership career spanning three decades in multiple sectors including several CEO roles.
WisdomLab contends that of all the classes of assets in an organisation, its People are the least understood, the most dismissed and provided the least maintenance. Vastly more and better knowledge and wisdom about People is in the Humanities, Sociology, Philosophy and Neuroscience than the Business Schools. For the past 15 years Errol has been translating this wisdom into organisations.
Simple Problem Solving - Addressing Problems & Issues Raised at Daily Review Meetings
Workshop Overview
At Daily Review Meetings we hear about problems or issues which have impacted on our ability to achieve our expected performance. As a result, we should initiate actions to firstly fix or contain the problem (if this has not already been done before the meeting), then most importantly, address how do we stop the problem or issue from happening again. This could involve a simple solution such as introducing a Preventive Maintenance task to stop a breakdown, to a more complex or Root Cause Analysis for example to determine why the machine component failed causing the breakdown after 4 years when it should have lasted 10 years. The key is to develop your people and your daily review meetings to be able to address all 3 scenarios.
Presenter: Ross Kennedy, Founder at CTPM - The Centre for Australasian TPM & Lean and NSW President at AME Australia
Ross, who is Wollongong NSW based, founded CTPM in 1996 after more than 20 years of manufacturing and operational experience covering maintenance, production, operations, and executive roles along with 5 years of international consulting experience.
Ross has been actively involved with Lean since 1985 and the application of Total Productive Maintenance (TPM) since 1990. In 1998 he developed and launched an Australasian version of the Japanese TPM methodology and the Toyota Production System (Lean) with a strong focus on Human Capital Development through On-going Improvement (a key driver of the Toyota Production System). Under Ross’s leadership, CTPM has assisted Manufacturing, Mining, Process Industries, Utilities and Service companies throughout Australia, New Zealand, Thailand, and Indonesia to strive for and achieve TPM & Operational Excellence.
12 Essential Elements to Supercharge Performance, Productivity and Profitability
Workshop Overview
“Solving day-to-day chaos doesn’t improve your business year-on-year.”
There is no shortage of ideas, yet implementation is a struggle. There are many problems and by trying to solve many, you solve none. You fly blind without critical insights, despite the data available. Growing the business with confidence and capability is an issue.
Learn what’s holding back your business / team from punching through productivity and performance.
Workshop outcomes:
- 12 Essential elements of a world-class Operational Excellence (OpEx) framework.
- Map your business’ current OpEx maturity
- Identify the key driver(s) that will provide you with the biggest boost in performance
Presenter: Ishan Galapathy, Managing Director at Capability Unlimited and Board Member at AME Australia
Ishan Galapathy is a productivity thought leader, author, speaker and mentor renowned for his simplified techniques. He has more than two decades’ experience with multinational companies within Asia Pacific. Ishan helps manufacturing businesses move from 'Chaos to Excellence' through productivity improvement programs and frontline leadership development programs. When he’s not working, you can find him playing backyard cricket with his sons or sipping a cup of coffee with his wife.