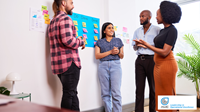
ONLINE WORKSHOP
Small Group Structured Problem Solving
Learn how to engage your team, solve problems, and embed lasting improvements in your workplace.
Description
As an individual, it can be quite challenging to figure out how to apply your ideas at work because they are integrated with those of others. Organisations that introduce company-wide processes to solve problems find that when a person’s work becomes their own, it becomes a rewarding workplace.
The purpose of this course is to make activities easier, simplify them and increase results. It is an informal approach that uses scientific methods from Quality Control Practices. This is presented in a form that is suitable for any work situation. This is a bottom-up structured approach to remove the things that irritate you in your work and, as such, is a foundational problem-solving methodology to increase motivation and introduce workplace communication methods. The steps presented are focused on three areas:
- steps to proceed with problem solving
- how to effectively summarise and visualise
- and finally how to present in a way that people understand.
These bookend the problem-solving method.
Course content
Pre-Work (15 minutes)
Log in to the Learning Management System and watch the pre-recorded videos.
Session 1 (60 minutes)
Setting up an activity board an gaining support to work on a theme and structuring the activity with an activity plan.
Session 2 (45 minutes)
Collecting, ideas, information and visualising it into a process flow and analysing the factors.
Session 3 (45minutes)
Allocation of roles and responsibilities and tracking progress of experiments.
Session 4 (45 minutes)
Checking the effect of your changes.
Session 5 (45 minutes)
Summarising and presenting your outcome as a standards.
Session 6 (60 minutes)
Next steps - embedding the learning into your workplaces and practices.
This course includes
- Six online sessions delivering theory and practical exercises in small, manageable bites.
- On-demand video
- Downloadable resources
- Certificate of completion
Requirements
-
None. We will work with you throughout the course
-
Some prior knowledge of Lean and continuous improvement is beneficial.
-
Course built to be open to all levels of the organisation.
-
Reach out to the facilitator if you need any assistance
Who Should Attend
This workshop is ideal for managers, team leaders, supervisors, and emerging leaders who are looking to:
-
Solve workplace problems more effectively and collaboratively
-
Improve team communication and engagement
-
Streamline processes and reduce daily frustrations
-
Build a culture of continuous improvement from the ground up
-
Learn practical tools they can apply immediately in their roles
Whether you're leading a small team or managing a department, this workshop will give you a simple, structured approach to drive meaningful change—without needing top-down directives or complex systems.
Instructor
BARRY MCCARTHY
Barry McCarthy’s career highlights include Plant Manager and Continuous Improvement Manager at Goodman Fielder and his most recent position with Toyota. Barry has worked with the Manufacturing, Sales and Corporate Arms of Toyota in Australia. With a grounded engineering background Barry has also implemented continuous improvement in food processing, manufacturing, packaging, printing, and front of house food service and management. In addition to the practical experience Barry has completed a Master degree in Applied Positive Psychology, Graduate Diploma in Business, Diploma of Training and Assessment, Diploma in Competitive Systems and Practices. Interestingly Barry’s first degree was civil engineering.
Other registration information
AME Australia is a not for profit association. We provide high quality low cost events.
You can become an AME member from $240.
This event may be cancelled by AME for any reason. AME is not responsible for incidental costs incurred by registrants.
AME may take photographs during events and may use those photographs for AME’s purposes.