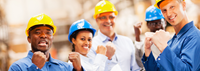
The Philosophy of Lean Thinking in Manufacturing
In the realm of manufacturing, where efficiency, quality, and continuous improvement are paramount, the principles of lean thinking have stood the test of time as a guiding light for success. Rooted in the concept of eliminating waste while maximising value, lean thinking has revolutionised the way organisations approach production processes, leading to streamlined operations, cost savings, and enhanced customer satisfaction.
Understanding Lean Thinking
At its core, lean thinking is a mindset that focuses on delivering value to customers through the relentless pursuit of efficiency. Originally developed by Toyota in the 1950s as part of the Toyota Production System, lean thinking advocates for the identification and elimination of all forms of waste, be it in the form of overproduction, excess inventory, defects, waiting times, unnecessary motion, or underutilised talent.
By embracing lean principles, manufacturers can achieve a state of operational excellence where every step in the production process adds value and contributes to the overall goal of meeting customer needs effectively and efficiently.
Key Principles of Lean Thinking
1. Value Stream Mapping
One of the foundational tools of lean thinking, value stream mapping involves visually depicting the entire production process to identify areas of waste and inefficiency. By analysing each step in the value stream, organisations can pinpoint opportunities for improvement and optimise the flow of work to enhance productivity.
2. Just-in-Time Production
The concept of just-in-time production emphasises producing goods only as needed, thereby reducing excess inventory and minimizing storage costs. By synchronizing production with customer demand, companies can operate more flexibly and respond quickly to changing market conditions.
3. Continuous Improvement
Central to lean thinking is the principle of continuous improvement, also known as Kaizen. This philosophy encourages employees at all levels to seek out incremental changes that lead to enhanced quality, efficiency, and customer satisfaction. By fostering a culture of continuous learning and innovation, organisations can stay ahead of the competition and drive sustainable growth.
Benefits of Implementing Lean Thinking
- Cost Reduction: By eliminating waste and improving efficiency, organisations can reduce production costs and enhance profitability.
- Improved Quality: Lean thinking helps identify and address quality issues early in the production process, leading to higher-quality products and increased customer satisfaction.
- Enhanced Employee Engagement: Empowering employees to contribute ideas for process improvement fosters a sense of ownership and engagement in the workplace.
- Faster Time-to-Market: Streamlining production processes enables companies to bring products to market more quickly, gaining a competitive edge.
Embracing Lean Thinking for Future Success
In an ever-evolving manufacturing landscape, where technology, consumer preferences, and market dynamics constantly shift, lean thinking provides a timeless framework for achieving sustainable success. By prioritising value, efficiency, and continuous improvement, organisations can navigate challenges, drive innovation, and deliver exceptional products that meet the needs of today's discerning customers.
Embrace the principles of lean thinking, and pave the way for a future where excellence in manufacturing is not just a goal but a reality.
Remember, in the world of manufacturing, the quest for perfection is ongoing, and lean thinking is the compass that guides us towards operational excellence.
So, are you ready to embark on a journey towards leaner, more efficient manufacturing processes? Let's start optimising your operations today!
Reach out to the AME Team to learn more.